Разширителни фугиса важен компонент на много тръбопроводни системи и са проектирани да увеличат гъвкавостта, да намалят напрежението и да компенсират движение, несъответствие, вибрации и други променливи.Ако еразширяванеставни повреди,ще бъдат причинени сериозни повреди и рискове за безопасността на тръбопроводната система.
Често използвани материали за разширителни фуги
Гумата има отлични свойства за абсорбиране на вибрации и ударни вълни и може да се използва за термично разширение. За защита на оборудване като помпи, разширителните съединения са идеални за намаляване на предаването на шум и вибрации от друго оборудване. Освен това, те могат да се използват като амортисьори за смекчаване на щети от сеизмични събития и колебания на налягането.
Технически оплетен маркуч от неръждаема стомана с гъвкава или метална облицовка е ефективен в приложения, където се изисква абсорбиране на удари или несъосност на тръбите в среда с високо налягане и висока температура.
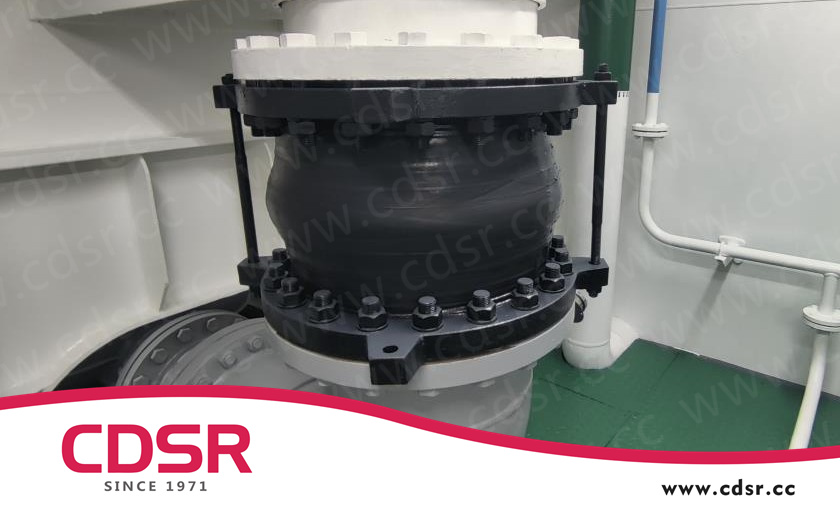
Възможни фактори за неуспех
Wдизайн на Ронг
Проектирането на разширителната фуга трябва да отчита околната среда и работните условия на тръбопроводната система. Ако проектът е неразумен, като например неправилен избор на материали или несъответствие в размерите, разширителната фуга може да се повреди поради невъзможността си да издържи на напрежението и налягането в системата.
Неправилна инсталация
По време на монтажа трябва да се спазват правилните стъпки и изисквания, включително правилната посока на монтаж, за да се предпази оборудването от повреда, в противен случай тръбопроводната система може да не работи правилно.
Неправилна поддръжка
Разширителната фуга изисква редовна поддръжка по време на употреба, като например проверка на уплътнителните свойства, отстраняване на запушвания и др. Ако поддръжката не е навременна или не отговаря на стандартите, това може да причини течове или повреди.
Контакт с хлорид
Разширителните фуги в определени специфични среди, като например контакт с хлорид, могат да причинят корозия или корозионна умора, което води до повреда. Хлоридите често се срещат в химически заводи и морска среда.
Дата: 18 декември 2023 г.